How We Work
Our manufacturing facility is equipped with cutting-edge machinery and testing apparatus, including laser cutting systems, automated welding machines, robotic mechanical polishing devices, CNC pipe bending technology, spectrometry, and X-ray detection equipment, all of which are pivotal for our operations.

1. Brewing Equipment

2. Auxiliary

3. Accessories

4.Services
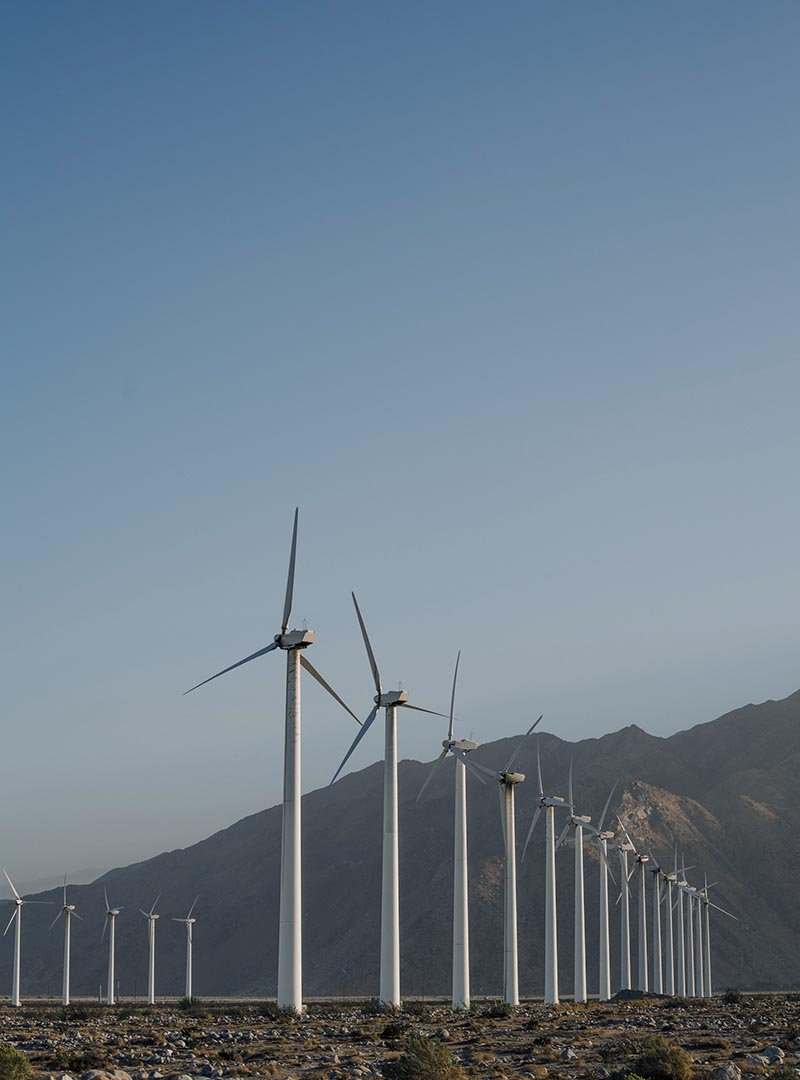
Manufacturing Process
Our brewing equipment stems from a perfect combination of exquisite craftsmanship and advanced technology. Starting with premium raw materials, each component undergoes a transformative journey through laser cutting, cylinder rolling, and dimple plate punching, ensuring accuracy and efficiency.
The meticulous process continues with automatic and TIG welding, fusing parts with unwavering strength and quality. Polishing refines the surfaces to a mirror-like finish, while precision measuring guarantees flawless assembly. Jacket welding and pressure testing reinforce the tanks’ resilience, preparing them for the rigors of the brewing process.
The culmination of all this precision production process is the final assembly, where auto piping welding integrates each element into a coordinated system. The result is a series of finished products that reflect our dedication to excellence, designed to elevate your brewery’s performance to new heights.
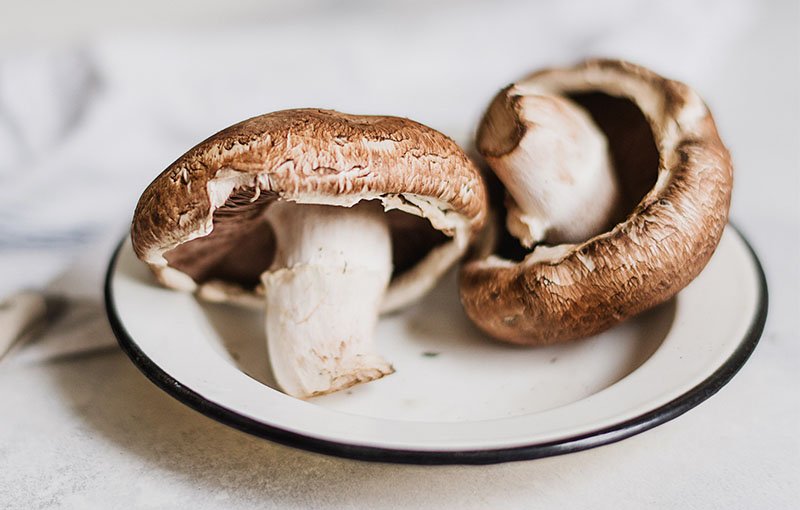
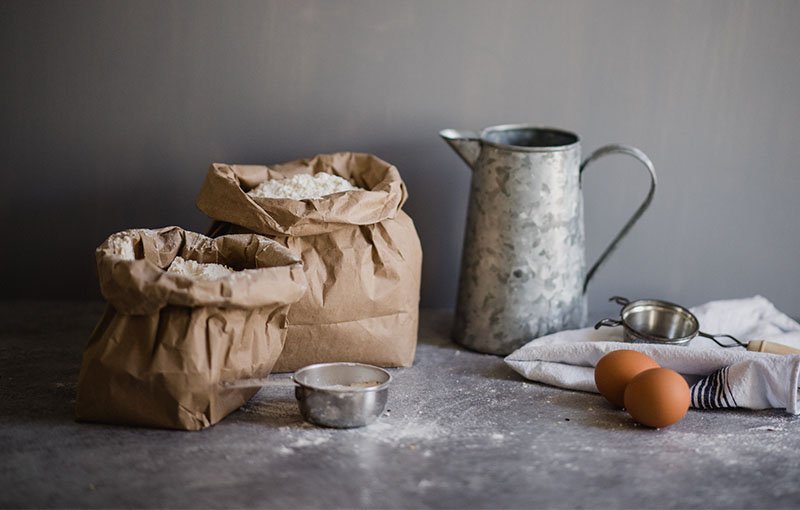
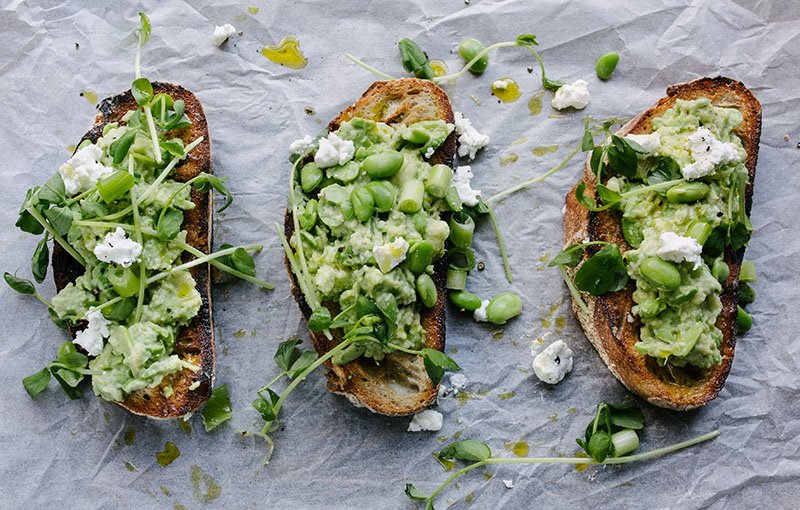
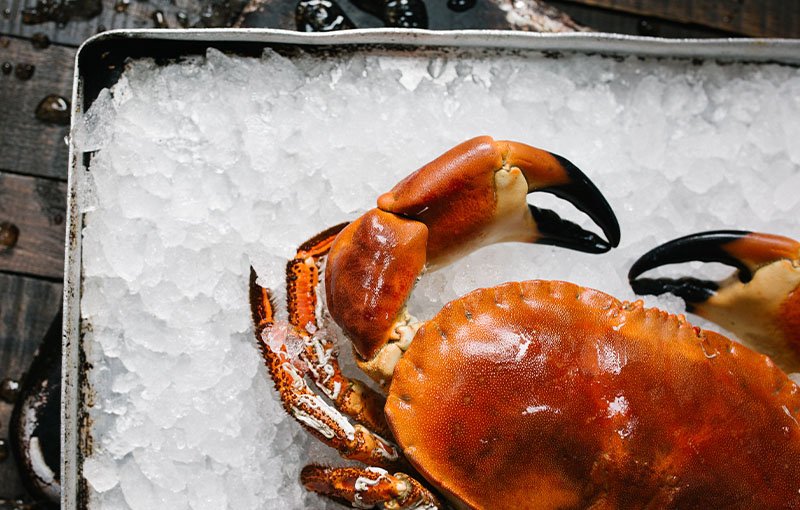
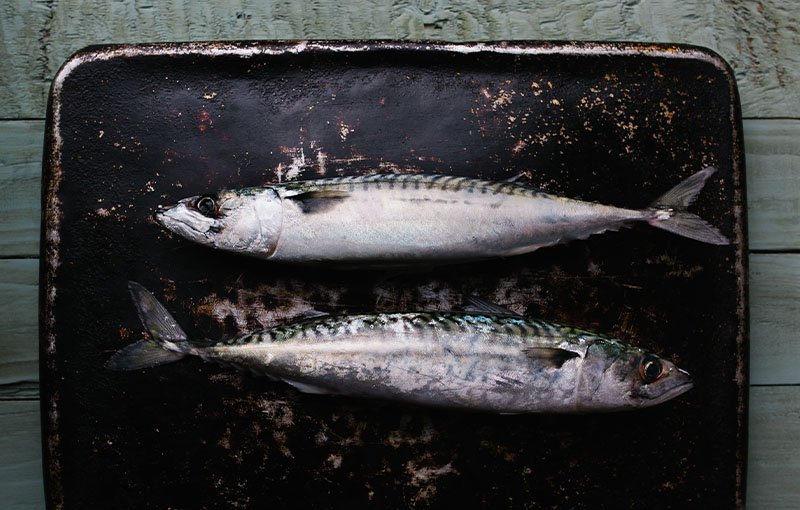
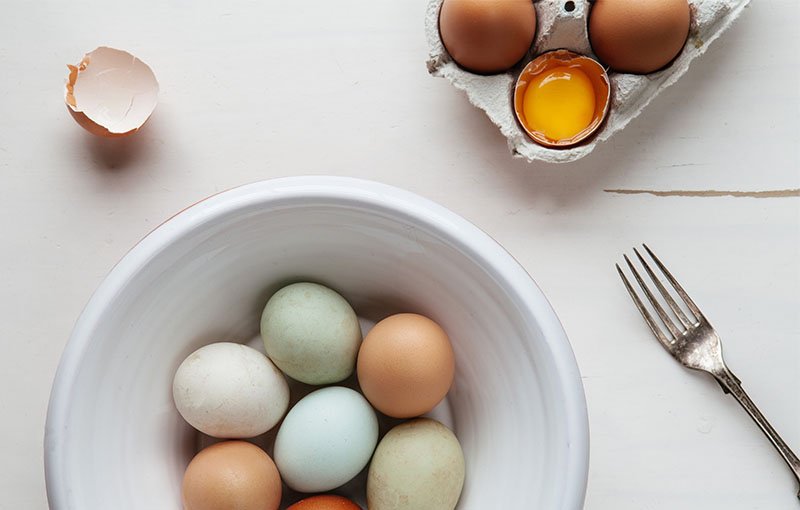
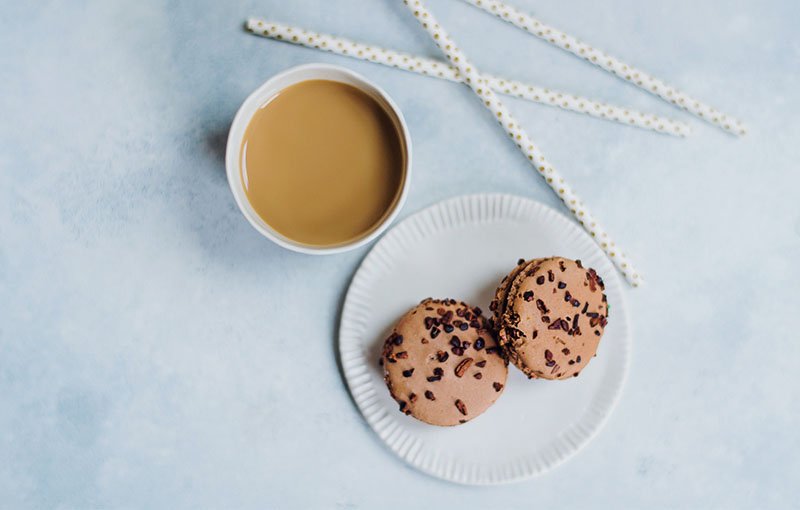
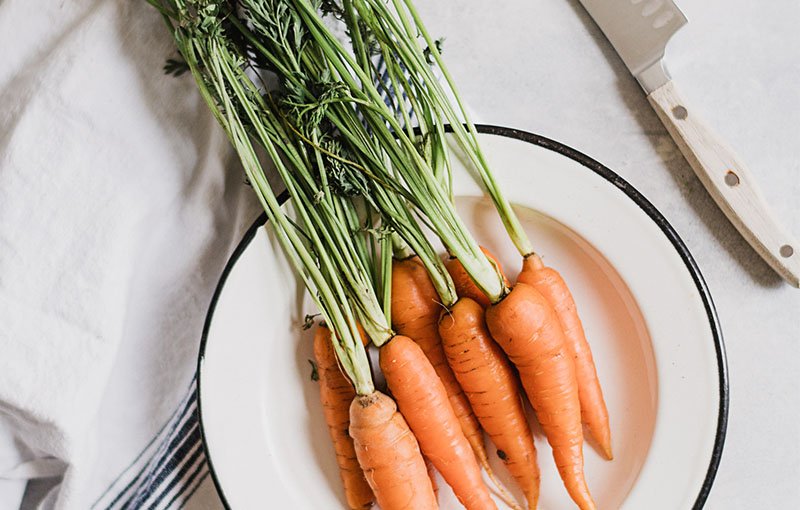
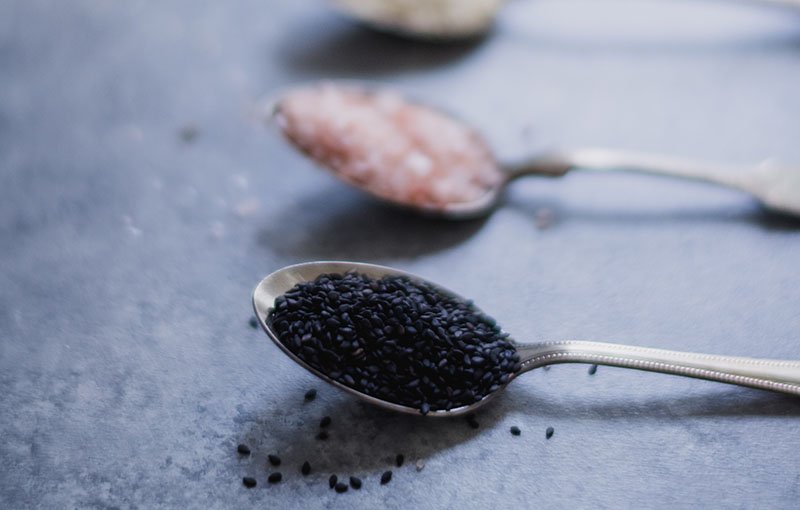
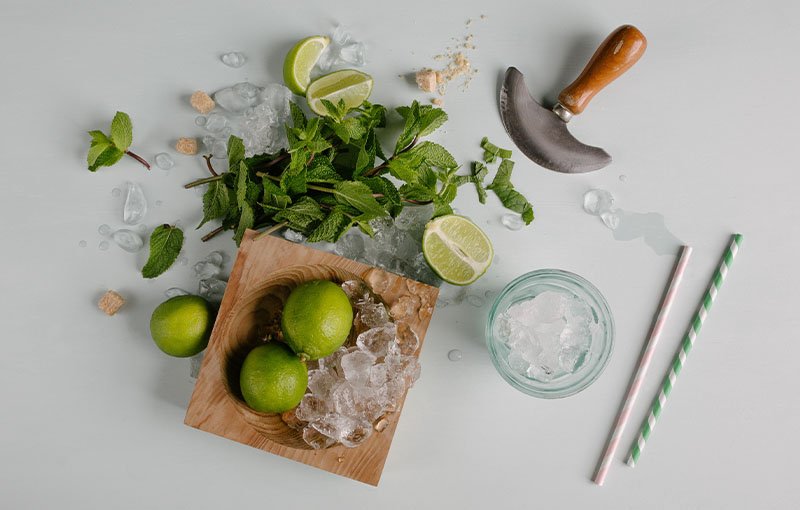
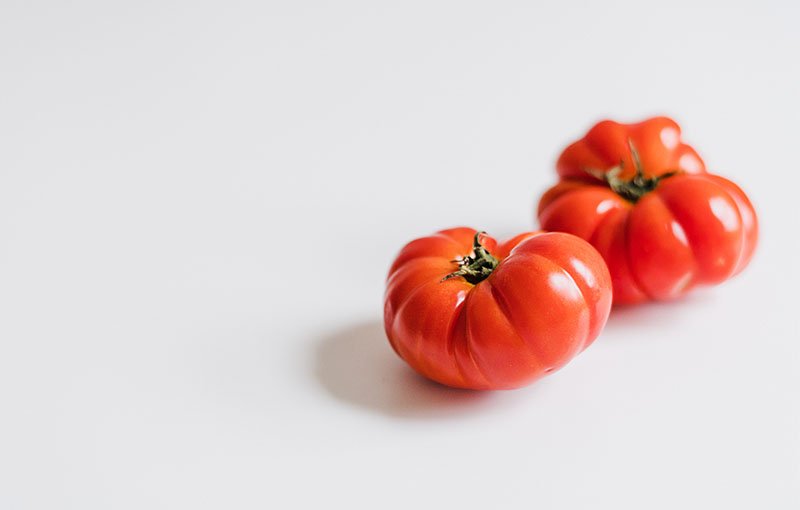
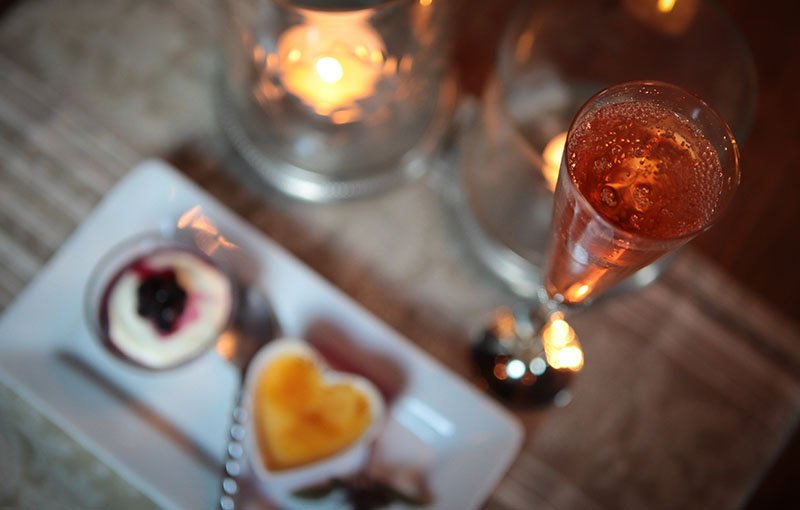
FAQ
1.Which kind of stainless steel does GAEA company use in the production of equipment?
GAEA company utilizes high-quality SUS304 stainless steel for its equipment. ‘SUS’ stands for Steel Use Stainless, indicating a grade that contains at least 18% chromium and 8% nickel, with a carbon content capped at 0.08%. This grade is chosen for its excellent forming and welding properties, robust corrosion and oxidation resistance, deep drawing capabilities, and ease of cleaning, ensuring our equipment is both durable and hygienic.
2.Can you provide technical support, drawings, installation services?
Absolutely. GAEA Company operates a comprehensive engineering department staffed with skilled CAD technicians. We are capable of delivering complete brewery layouts tailored to your specific space requirements, including Process and Instrumentation Diagrams (PIDs), electrical schematics, piping layouts, and detailed individual equipment drawings.
For the installation phase, we offer on-site technical support. Our team will dispatch a qualified technician to assist with your brewery setup. The associated fee is calculated based on the project’s duration, scale, and complexity, ensuring you receive personalized and efficient installation services.
3.Does GAEA have standard designs or can you customize to my specifications?
GAEA offers both standard and fully customizable solutions to meet your unique requirements.our team at GAEA Craft is dedicated to manufacturing custom brewhouses and tanks that cater to a diverse range of industries.We specialize in custom fabrication and design, allowing us to work closely with you to either realize your design vision or develop a tailored solution that addresses your specific needs.
4.What is the lead time for ordering?
The lead time for your order depends on its complexity. Generally, we aim to complete manufacturing within a range of 60 to 100 working days after receiving your order.
5. If I decide to purchase from GAEA, what are my payment options and terms?
At GAEA, we offer a variety of flexible payment options to accommodate your needs. These include:
Wire Transfer (TT): A direct bank-to-bank transfer for secure and efficient payments.
Western Union: A quick and reliable money transfer service.
Letters of Credit (L/C): A secure trade finance instrument provided by banks.
Trade Assurance: A service that offers protection for both buyers and sellers in transactions.
Our standard payment terms require a 40% down payment after the signing of approved drawings. The remaining 60% balance is due just prior to shipping, ensuring a smooth transaction process for both parties.
6.Am I able to see my equipment in person, possibly running a brew to test functionality?
Yes, we understand the importance of seeing your equipment firsthand.We also warmly welcome you to visit our factory to tour our operations and view your equipment up close.Our new factory is equipped with 5G-enabled technical WiFi, Also allowing you to virtually “see” your equipment during production via a webcam.
Furthermore, you have the option to hire a third-party inspection company to thoroughly review your system and provide valuable feedback before the equipment is shipped. This additional layer of inspection ensures you receive a product that meets your expectations and requirements.
7.Can you manage and coordinate shipping and delivery to my brewery location?
Absolutely. GAEA provides a comprehensive one-stop solution that encompasses every aspect of shipping and delivery to your brewery location. Our services include:
Documentation: We handle all the necessary paperwork to ensure a smooth process.
Ocean Freight: We arrange for the safe and efficient transportation of your equipment via sea.
Customs Brokerage: We assist with customs clearance to avoid any delays.
Inland Freight: We manage the overland transportation to your specified destination.
LTL Trucking Services: We offer Less-than-Truckload shipping for cost-effective delivery.
Simply provide us with your destination details, and we will take care of the rest, ensuring your equipment arrives safely and on time.